Firmy by měly výrazněji zareagovat na zlevnění energií, materiálů a dalších nákladů a snížit finální ceny svých výrobků, říká Jan Lát, spolumajitel slévárenské firmy Beneš a Lát. „Jakmile se otevře příležitost chytit větší žvanec, tak ho hodně firem chytí, ale pak už nereagují na opačný trend. Myslím si, že to do značné míry způsobuje vysokou inflaci v celé Evropě,“ dodává. V tomto ohledu kritizuje zejména evropské automobilky.
Vaše firma vyrábí odlitky ze slitin hliníku a zinku a výlisky z plastů. Pro jaké obory pracujete nejvíc?
O první místo se přetahuje výroba nákladních aut a vlaků, na třetím místě je automobilový průmysl. Každý z těchto segmentů se na našich tržbách podílí asi 20 procenty. Také hodně vyrábíme díly pro hydrauliku, manipulační techniku a další stroje. Kdysi to tak nebylo, hlavním segmentem byly firmy z automotive. Zhruba od roku 2004 jsme postavili strategii na tom, že nedodáváme jednomu segmentu. Šli jsme proti proudu ve chvíli, kdy tady prakticky všichni adorovali – a do dneška to poměrně nepochopitelně trvá – automobilový průmysl. My ale na něm, ani na jiném segmentu, nechceme být závislí, proto žádný nesmí tvořit více než čtvrtinu a žádný zákazník více než 15 procent našeho obratu. Že se to vyplácí, se poprvé ukázalo v letech 2008 a 2009, když přišla krize. Tehdy padl nejdřív „na pusu“ automotive, postupně klesly i další obory a zase se zvedaly. Výpadky tak přicházely postupně a neochromily nás najednou tak jako dodavatele, kteří vyrábějí převážně pro automotive. To se opakuje v každé krizi. Ta současná je ale podivná, nasedá na sebe jeden problém za druhým. Nejdřív přišla pandemie, pak zdražily čipy a suroviny, potom vystřelily energie a jako zatím poslední přišla válka na Ukrajině.
V minulém fiskálním roce od dubna 2021 do března 2022 jste měli obrat 869 milionů korun a zisk 17 milionů korun. Loni v listopadu jste říkal, že vaše výroba klesla o třetinu. Jak nakonec dopadl váš poslední finanční rok?
Obratově to bude velmi podobné, kolem 850 milionů korun, a zisk dopadl o něco lépe než v minulém roce, protože jsme dokázali významně ořezat spotřebu energií i další náklady, zároveň jsme dokázali do prodejních cen začlenit energetickou přirážku. Tento výsledek je ale jen finanční pohled. Obrat se nakonec vyšplhal tak vysoko díky tomu, že vylétly ceny materiálů a energií. Fakticky šla výroba dolů skoro o třetinu.
Nejpodivnější je, že poslední dva až tři roky máme při poklesu výroby největší objem nově získaných zakázek.
A jak vypadá letošní rok?
Jednotlivé segmenty si sedají už tři roky. V roce 2008 byla krize sice hluboká, ale krátká, a teď je to jinak. Automobilový průmysl se po propadu během covidu dodneška úplně nevzpamatoval. Postupně klesla i výroba nákladních aut a také vlaků. Producenti vlaků přitom dřív dlouhodobě nestíhali vyrábět podle poptávky a jejich zakázky byly zpožděné i o dva roky. Dneska už vyrábějí na sklad. Trh se úplně otočil.
Jaké máte signály z trhu o dalším vývoji?
Situace je velice nečitelná. Překvapivě se objevuje o něco víc objednávek na srpen a září, ale zatím nevidíme, že by mělo dojít k většímu obratu. Nejpodivnější je, že poslední dva až tři roky máme při poklesu výroby největší objem nově získaných zakázek. Náš cyklus od domluvy se zákazníkem do zahájení sériové výroby trvá asi devět měsíců. Nejdřív na produktu pracují konstruktéři a designéři, vytvoří prototyp, pak se pro sériovou výrobu vyrábí forma a potom čekáme na objednávky sériové výroby. Do sériových dodávek ale nabíhá v posledních letech jen velmi malá část produktů z nově vyrobených forem. Dřív jsme vyráběli řádově padesát forem pro nové produkty ročně, ale za poslední dva roky je to bezmála dvojnásobek. Jenže pro skutečně sériovou výrobu se jich využilo jen kolem 20 procent. Dřív to byla naprostá většina ihned po dokončení formy. A to jedna forma stojí i ke dvěma milionům korun.
Chytí a nepustí
Čím to je, že zákazníci tolik investují do přípravy a pak sériovou výrobu nechtějí?
Vnímám to tak, že firmy odkládají uvedení nových produktů do budoucna. Při náběhu nového produktu vždycky přicházejí určité vícenáklady. Asi je pro firmy teď jednodušší vyrábět staré produkty, které nějak fungují, než se pustit do nejistých novinek. Nejspíš se bojí riskovat. Máme i zákazníka, který u nás nainvestoval za poslední rok přes 20 milionů korun do forem pro sériovou výrobu dílů, ale moc se jich zatím nepoužilo jinak než na ověření funkčnosti. Firmy jsou hodně opatrné, nechtějí rozhodovat pod tlakem a vyčkávají, co se bude na trhu dít.
Nemůže to být i tím, že jste drazí? Ceny surovin, se kterými pracujete, tedy hliníku a zinku, během pandemie vyletěly vzhůru, ale teď už rok klesají. Snižujete i ceny výrobků?
Ceny materiálů, ale i energií se do cen výrobků promítají přes indexaci v závislosti na vývoji cen na burzách, takže energetickou složku cen snižujeme už třetí kvartál a materiálovou čtvrtý kvartál. Tím pádem klesají i naše finální ceny – jsme zpět na úrovních poloviny roku 2021.
Jsem skeptik vůči evropskému automobilovému průmyslu. Tento byznys je strašně surový vůči dodavatelskému řetězci.
Říkal jste, že jste se odpoutali od závislosti na automobilovém průmyslu. Podle vás tento trh po covidu stále nenastartoval, ale výroba aut za prvních pět měsíců vzrostla o čtvrtinu. Nezaměříte se teď víc na autoprůmysl?
Pořád se v Česku vyrobí mnohem méně aut než před pandemií covidu. Propad byl obrovský a dlouhý, takže současné oživení není dostatečné, aby propad pokrylo. Navíc jsem trochu skeptik vůči evropskému automobilovému průmyslu. Tento byznys je strašně surový vůči dodavatelskému řetězci, s dodavateli probíhají velice tvrdá vyjednávání. Na menším dílu, třeba na tlačítku palubní schránky, je automobilka schopna nás do zblbnutí drtit o desetiny i setiny centů. Přitom jen na výrobu forem pro tento prvek u nás zbytečně vyhodila 300 tisíc eur.
Proč zbytečně?
Protože pak zjistili, že když se všechno sestaví dohromady, nefunguje to dobře. Do toho se v automobilce vyměnil hlavní designér a řekl, že ten čudlík nebude promáčklý, ale vypouklý. Všechny hotové formy se po půl roce práce a vývoje vyhodily a udělali jsme nové. Otázka je, kolik peněz utratili za formy pro další díly, které se také vyhodily. Takže víte, že automobilka zbytečně vyhodí miliony eur na vývoji auta, aby pak peníze dostala z dodavatele, kterého drtí na každém čudlíku. Myslím si, že evropský automotive má obrovský problém.
Jen kvůli vyhozeným penězům za formy, nebo vidíte i další potíže?
Další věc je, že evropský automobilový průmysl je poslední roky tlačený Evropskou unií a regulacemi k něčemu, co americký i čínský automotive udělal i bez regulace. Podívejte se, kolik čínských dodavatelů elektromobilů už dneska dodává do Evropy. Kdyby nepřišla Tesla a regulace, evropské automobilky by dodnes o výrobě elektromobilů jen mluvily. Evropský automobilový průmysl se buď velmi rychle probudí, nebo postupně zanikne.
Co by měly evropské automobilky změnit?
Přestat povídat o tom, jak jsou zelené a něco vyvíjejí, ale skutečně to dělat, a to aniž by zbytečně vyhazovaly peníze. I proto jsou evropské elektromobily drahé. Dnes do Evropy přicházejí čínské elektromobily, které stojí kolem poloviny toho, co srovnatelný model od Škodovky.
Kdyby nepřišla Tesla a regulace, evropské automobilky by dodnes o výrobě elektromobilů jen mluvily.
V Číně je ale stále v řadě oblastí levnější pracovní síla, i když rozdíl s Evropou se už hodně smazal, a také čínská vláda výrobu elektromobilů dotuje.
Levnější pracovní síla už nehraje roli, naše díly jsou dnes cenově konkurenceschopné s Čínou. A malý Volkswagen stojí prakticky stejně jako Tesla vyrobená v Americe, kde není levnější pracovní síla než v Evropě. Myslím si, že to ani není dotacemi.
Čím to tedy je?
Je to vyšší efektivitou. Například nevyhazují ve vývoji zbytečně peníze za designové detaily. Pak je také rozdíl v technologické konkurenceschopnosti. Podívejme se na evropské automobilky a Teslu. Máme elektrického Golfa s dojezdem 200 kilometrů a jen o něco dražší Teslu s dojezdem 500 kilometrů. Evropské elektromobily buď nemají slušný dojezd, nebo jsou drahé. Přesto tu automobilky zvedly ceny nesmyslně vysoko. Argumentovaly zdražením energií, čipů a podobně, ale nezaznamenal jsem, že by ceny aut šly po snížení nákladů dolů. My jsme díky poklesu cen energií a materiálů zlevnili, a to i vůči automobilkám. To je další rozměr, jak si Evropa ubližuje. Jakmile se otevře příležitost chytit větší žvanec, tak ho hodně firem chytí, ale pak už nereagují na opačný trend. Myslím si, že to do značné míry způsobuje zbytečně vysokou inflaci v celé Evropě.
Vyrábíte převážně na export. Jaký podíl vašich produktů jde za hranice?
80 procent výroby jde napřímo do zahraničí a včetně nepřímého vývozu, kdy výrobek někdo z Česka zpracuje a prodává dál za hranice, je to přes 95 procent. Největšími trhy jsou pro nás Maďarsko, Polsko a Německo. Maďarští i polští odběratelé jsou ale navázáni hlavně na Německo.
Německo je hlavní vývozní trh pro většinu českých výrobců, průmyslová výroba tam ale nyní stagnuje a HDP země letos nejspíš poklesne. Co to znamená pro český průmysl?
Umíme s tím žít, možná to nebude úplně veselý rok, ale nemyslím si, že by měl ještě přijít dramatický propad, spíš předpokládám stagnaci. Z ní vede cesta. Celý výrobně‑dodavatelský řetězec by se měl vrátit nohama na zem. Firmy by měly zareagovat jednak na to, jak klesla kupní síla lidí, a pak také na to, že vstupní náklady objektivně nejsou na takové úrovni jako před rokem nebo rokem a půl, a měly by proto snížit finální ceny.
Tiskneme z kovu
Označujete se za technologickou firmu. Co to v podání slévárny a lisovny znamená?
Máme vlastní IT oddělení, které pro naše potřeby vytvořilo systém pro řízení výroby. Se sběrem dat z výroby jsme začali už v roce 2008. Od té doby máme souvislá data o každé operaci, každém zaměstnanci, jeho práci, co proběhlo dobře a co špatně. Na tom je také postavený odměňovací systém. Postupně se na sběr dat a vývoj systému nabalovaly i další technologie. Děláme třeba za pomoci umělé inteligence predikci poruch na strojích.
Už pár let se také zabýváte 3D tiskem. Je to kvůli prototypům?
Máme i 3D tiskárnu na plastové prototypy, ale hlavně tiskneme z kovů. Začalo to tak, že nám chyběla vlastní laboratoř na prvotní vývoj. Na takovou investici jsme stále ještě malá firma. Tak jsme v roce 2016 založili spolu s Fyzikálním ústavem Akademie věd a Českou zbrojovkou dceřinou firmu Cardam. Pro tuto spolupráci jsme u nás zainvestovali i do 3D tiskárny. Umíme tisknout z hliníku, oceli, nerezu, titanu nebo mědi. Tiskárna je primárně určena pro vývoj, typické využití pro naše potřeby je 3D tisk forem pro slévárnu, ale pro některé zákazníky na ní děláme i díly pro sériové dodávky.
Jan Lát (41)
Už během studia na Vysoké škole ekonomické v Praze vstoupil do rodinné firmy Beneš a Lát jako IT podpora, prošel oddělením nákupu a od roku 2012 je finančním ředitelem. V roku 2007 se po úmrtí otce stal spolu se svými sourozenci spolumajitelem firmy a místopředsedou představenstva. V roce 2021 získal titul Manažer roku.
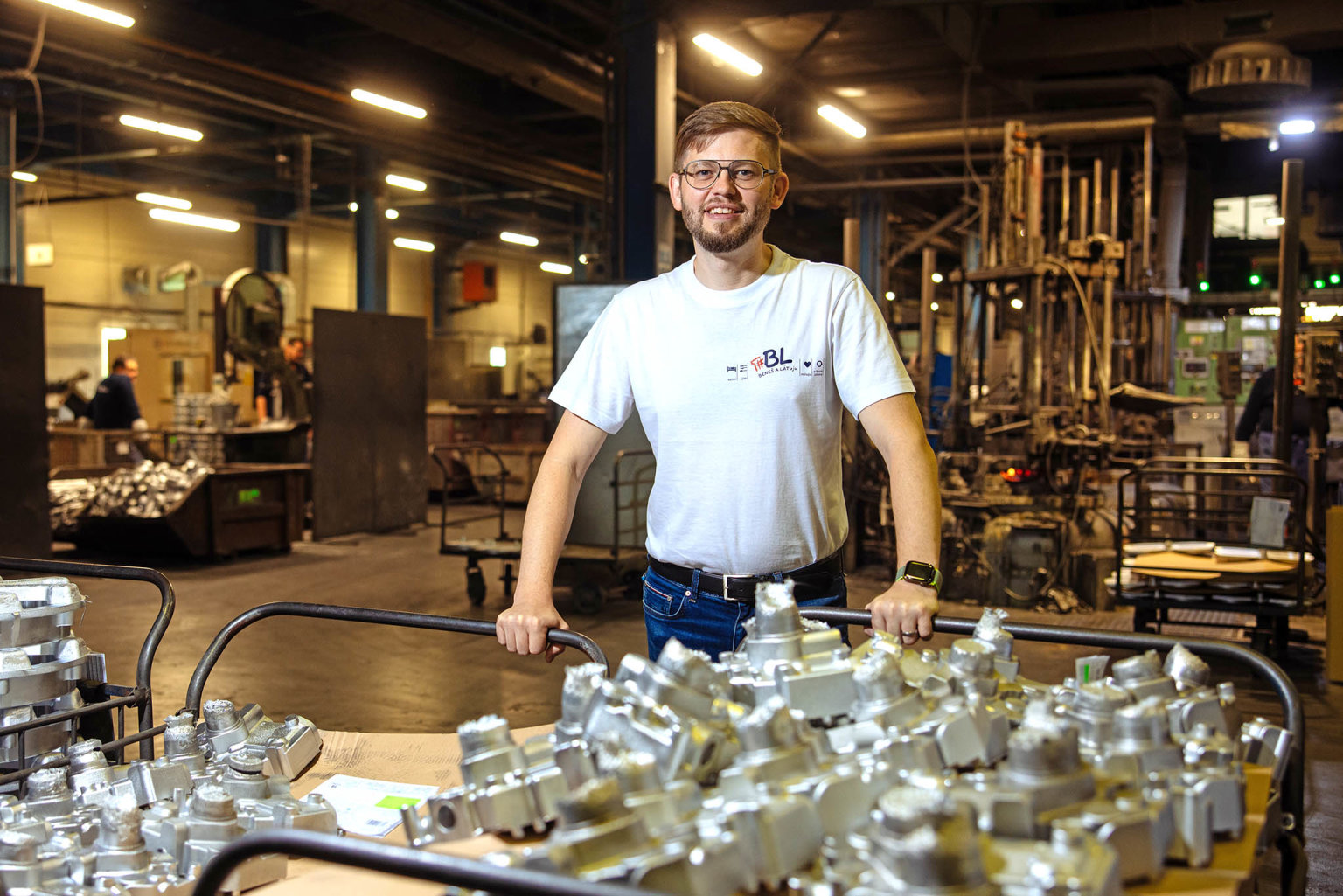
Je běžné, že je firma slévárna kovů a zároveň lisovna plastů jako vy?
Úplně běžné to není. Viděli jsme v tom obrovskou výhodu, protože naše produkty ze zinku se často pojí s plastovými kryty. Když jsme v roce 2005 otevřeli zinkovou slévárnu kousek od Semil a hlásila se nám spousta techniků, zjistili jsme, že prchají z nedaleké krachující lisovny plastů. Tak jsme ji převzali. Díky tomu jsme získali nové zákazníky a také výrobu stavebnic a her pro děti.
To je ale dost odlišný obor od segmentů, do kterých dodáváte.
Vyráběly se tam tradiční české hračky jako stavebnice Seva nebo autíčka Monti System, které pomáhají dětem se rozvíjet. V té době už jsme začali vnímat, že se děti přesouvají k mobilům. My ale potřebujeme konstruktéry a techniky s představivostí. Pro řemeslo je potřeba dítě nadchnout včas, a ne až když mu je patnáct. Takže investice do výroby stavebnic pro nás byla investicí do budoucnosti.
Kadeřníci ve slévárně
Vaše firma vznikla v roce 1934 jako Slévárna a strojírna J. Beneš. Založil ji Josef Beneš, který padl při Pražském povstání, a jeho manželku Andělu Benešovou si vzal Josef Lát. To byl váš děda?
Ano, firmu založil pan Beneš, náš nevlastní děda, pak ji od roku 1946 do roku 1980 řídil vlastní děda a od roku 1985 zase jeho syn, tedy náš táta. Proto jsou v názvu firmy jak zakladatel, tak jeho pokračovatelé, kteří firmu významně posunuli.
Od založení ve třicátých letech vedli vaši firmu včetně komunistického období – jen s pětiletou pauzou – vaši příbuzní. Jak se to podařilo?
Je to hodně velká anomálie. Dominantní roli v tom hrají dva vlivy. V roce 1948 byla fabrika znárodněna. Za války babička s panem Benešem do slévárny dostali desítky lidí, kteří by jinak byli totálně nasazeni v Říši. V továrně se tak najednou ocitli kadeřníci, pekaři a další živnosti, které byste tam asi nehledal. Po válce závodní rada ROH vydala babičce potvrzení, koho s dědou zachránili. Druhý vliv byl ten, že když děda Beneš padl na barikádách, dostal in memoriam Československý válečný kříž 1939. Vdovu s tímto vyznamenáním a historií zachráněných sousedů komunisté neperzekvovali. Navíc děda Lát nebyl vlastník fabriky. Znárodnili ji babičce, takže byl vlastně jen najatý manažer, který dělal ředitele. A v této pozici ho komunisté docela překvapivě nechali.
Evropské elektromobily buď nemají slušný dojezd, nebo jsou drahé. Přesto tu automobilky zvedly ceny nesmyslně vysoko.
Dnes jsou v představenstvu firmy jak Látovi, tedy vy a váš bratr, tak Jakub Beneš. Je to shoda jmen, nebo je příbuzný se zakladatelem?
Ano, je to vnuk pana Beneše, a tedy můj nevlastní bratranec. Ve firmě pracuje od roku 1996 s dvouletou pauzou, kdy z pozice ředitele jednoho z našich závodů odešel do fyzikálního ústavu připravovat projekt nového inovačního centra B4I v Dolních Břežanech. Dnes je v rozvojovém týmu společnosti, a jak jste zmínil, i v představenstvu.
Firmu ale vlastní jen Látovi. Po smrti vašeho otce jste se majiteli stali vy, váš bratr a sestra.
Otce z fabriky jako ředitele z komunistického období v roce 1990 vyhodili. Dalo by se čekat, že po revoluci znárodněnou fabriku dostanou zpátky v restitucích potomci původního vlastníka. Podle restitučního zákona se ale vracelo jen to, co rodina vlastnila původně, tedy bez významných investic v mezidobí. Děda i táta se ale k fabrice chovali, jako by to stále byla jejich rodinná firma, a rozšiřovali ji. Proto se z fabriky v restitucích vracela jen malá část, asi desetina, a proto táta musel napsat privatizační projekt. To se mu povedlo a v roce 1992 získal fabriku zpátky do rodinných rukou, respektive do rukou tří bratrů, dvou Látů a jednoho Beneše. Všichni ale nebyli zvyklí na rozdělení manažerských rolí a navzájem si zasahovali do kompetencí. Po několika letech ve ztrátě se v roce 2002 domluvili na vypořádání, takže otec nakonec získal celou firmu.
Vy ve společnosti pracujete jako finanční ředitel, váš bratr jako obchodní ředitel a sestra je v dozorčí radě. Proč není někdo z vás tří majitelů generálním ředitelem?
Vlastnickou strukturu a výkonný management oddělil už kdysi táta, právě proto, že spolumajitelé a zároveň manažeři příliš nectili rozdělení rolí. A pro nás to byl skvělý odstrašující případ. Myslím, že i díky tomu to teď mezi námi sourozenci funguje. Náš model řízení stojí na tom, že máme svého šéfa – ředitele – a jako majitelé musíme být konzistentní v tom, že nepřekračujeme své kompetence a nezasahujeme mu do řízení.